Specialty materials for corrosive pumping
...are you selecting the right material?
Across industries, corrosion is one of the major burden causing considerable expenses in maintenance costs, spare parts inventories, downtimes and even shutdowns. Prior to deciding on the materials of construction for your pumping system, you should have a full understanding of the pumped fluid characteristics and operation conditions in order to prevent and minimize corrosion. The compatibility of a material with the fluid is essential to achieve the reliability expected and proper performance.
Corrosion is difficult, or even impossible to avoid in pumping industry, however it is possible to control and reduce the damages in elements exposed to corrosion and the costs related to fix them with the right material selection.
Harsh environments require the application of corrosion-resistant materials in your pumping equipment, especially for the components that come into contact with the pumped liquid. Because of our expertise in the field of fluid transfer technology, our extensive knowledge in corrosion and wear resistant materials and our permanent dialogue with the customer, Ruhrpumpen is able to provide centrifugal pumps constructed of specialty alloys such as titanium, zirconium and Nickel Based Alloys (Inconel and Hastelloy).
Whether it is in verticals, horizontals, submersible or reciprocating pumps (among others), we can deliver the solutions that maximize efficiency and minimize the risk of serious and costly disruptions in the most difficult and critical services of the industry.
Special materials for special requirements
Titanium
Thanks to technological advance, titanium is now a viable option where conventional steel materials would render useless due to corrosion. Despite its high cost, its physical and chemical properties turn titanium into a cost-effective solution for harsh and corrosive industrial applications where long-term reliability is crucial.
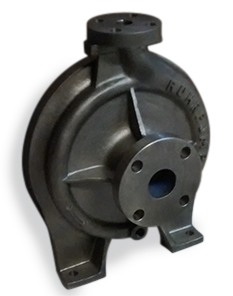
The physical properties of titanium include a remarkable strength-to-weight ratio in comparison with other metals. It is as strong as steel but almost half the weight. At the same time, its passive oxide coating makes it extremely resistant to corrosion by saline solutions and virtually unaffected by most oxidizing acids and industrial chlorine solutions. This makes titanium the best option for applications in desalination plants, marine and offshore applications, chemical plants and wastewater treatment plants, just to name a few examples.
Other applications include:
- Bromine feeders
- Seawater boosters
- Sodium hypochlorite
- Hypochlorite dosing
- Polymer feed
- Fertilizers
- Acid regeneration plants
Zirconium
Very similar to titanium, zirconium is extremely resistant to heat and corrosion. Zirconium alloys are widely used in factories that make reactive materials. Moreover, its passivating oxide layer makes it resistant to practically all organic acids and alkaline solutions as well as to mineral acids.
The properties make the material suitable for a wide range of applications in chemical engineering, especially in sulfuric and hydrochloric acid applications. However, zirconium is less suitable for applications such as: handling hydrofluoric acid, sulfuric acid in concentrations exceeding 70%, aqua regia, wet chlorine gas, iron(III) chloride and copper(II) chloride.
Zirconium applications include:
- Acetic acid production
- Urea production (stripper)
- Nitric acid applications
- Sulfuric acid applications
- Methionine production (cattle food additive)
- Formic acid environments
- Strongly alkaline environments
- Hydrochloric acid, excluding ferric and cupricions
- Salt solutions
- Organic
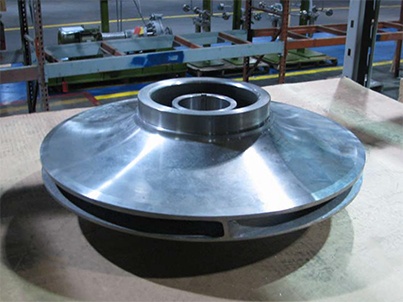
Inconel or Hastelloy
Nickel-based alloys with exceptional resistance to stress corrosion, they are also able to withstand both oxidizing and non-oxidizing acids and resists pitting and crevice attack in the presence of chlorides and other halides.
Very resistant materials to corrosive media, they are suitable for most chemical process applications in the as-welded condition. These materials can handle hot contaminated mineral acids, organic and inorganic chloride-contaminated media, chlorine, formic and acetic acids, acetic, acetic anhydride, seawater and brine solutions.
- Flue gas scrubber systems
- Nuclear fuel processing
- Phosphoric acid production
- Sulfur dioxide cooling towers
At present, there are multiple material options able to reduce or minimize the corrosion effects with very good results; however, these options are increasing as more specialty alloys are brought to the market. Over the years, pumps handling corrosive fluids have been constructed from Standard and Nickel Austenitic cast-irons or even from aluminum-bronzes, but it must be admitted that super duplex alloys, nickel-based alloys and titanium alloys are the preferred ones when price is not an issue.
Quick reference chart. Download this brief chart illustrating some corrosive media and if the material is recommended.
pdf Specialty materials for corrosive pumping - Quick Chart (265 KB)
Contact a Ruhrpumpen specialist for advice on final material selection.